The Contractor’s Quick Guide to Roof Finishes
We get it, you get it: every single roofing project comes with its own set of unique demands. In many cases, contractors find themselves at a crossroads where aesthetics, practicality and deliverables must meet. For you, this means that your choice of roof finish is key in finding the right balance. In our latest learning resource, we make this decision easier than ever by exploring three standout roof finishes: green roofs, standing seam profiles and ballasted roofs.
Whether the goal is to create a visually striking feature, a highly functional design, or a seamless combination of both, the right roof finish can make all the difference. Depending on the nature of your project, finding a solution to meet the needs of designers, installers and building owners is absolutely achievable. To start, let’s take a look at green roofs; their benefits and applications.
Green Roofs: The Sustainable, Aesthetic Choice
Green roofs – also known as living roofs – have seen a huge upsurge in popularity over recent years, and from a building owner’s perspective, it’s not hard to see why. Unlike any other roofing finish, this choice offers a perfect blend of beauty, functionality and sustainability. This, among many other reasons, makes green roofs the standout choice for modern construction professionals.
Green roofs are highly popular choices for both residential and commercial projects. Here at Tecron, we’ve found that green roofs are particularly effective in built-up urban environments where green spaces are limited. Beyond that, they’re an essential when it comes to achieving sustainability certifications such as LEED and BREEAM. So, what makes green roofing so appealing?
- Visual appeal: Green roofs transform what would otherwise be a barren, functional surface into a lush, visually striking feature. For buildings in urban environments, they provide a much-needed touch of greenery, softening the harshness of concrete and steel.
- Biodiversity & habitat creation: By cultivating a natural habitat, green roofs support flora and fauna that might otherwise struggle to thrive in built-up areas. They attract pollinators like bees and butterflies, contributing to the local ecosystem and promoting biodiversity.
- Rainwater management: One of the critical roles of green roofs is their ability to manage rainwater effectively. In urban areas prone to heavy, tropical-like rainfall, green roofs help reduce stormwater runoff by absorbing and retaining rainwater. This reduces the pressure on drainage systems and minimises the risk of flooding.
- Improved thermal performance: Green roofs act as natural insulators, reducing heat transfer and improving energy efficiency in buildings. They help keep interiors cooler in summer and warmer in winter, lowering energy costs and contributing to sustainability goals.
Standing Seam Profiles: Timeless Results on a Budget
While green roofs are a strong choice, they are also one of the most costly. Where you’re faced with a more budget-limited project, standing seam roofs present a strong alternative. Traditionally associated with high-end materials like zinc and copper, the cost today of installing genuine metal standing seams can be too high to bear. Fortunately, standing seam profiles offer a more financially-accessible way to replicate this iconic style.
Standing seam profiles can be added to a roof’s waterproofing later, and do a great job of mimicking the visual effect of zinc or copper seams. Luckily for our customers, they can be applied to materials such as Fatra PVC membranes or Polyroof liquid waterproofing systems as a strong, customisable solution. This choice is particularly effective for buildings aiming to combine modern performance with classic design elements.
Below, we’ve listed four of the key benefits you can expect when working with standing seam profiles:
- A budget-friendly choice: Forget using costly zinc or copper – standing seam profiles allow you to achieve that high-end appearance without absorbing the significant costs of investing in these materials.
- Beautiful aesthetics: Whether your customer wants a classic, traditional style or something more sleek and modern, this choice of roof finish can be tailored to meet either objective. This makes them a popular choice among architects looking for ways to enhance a building’s visual appeal.
- Easy to use: Adding these profiles to a waterproofing system is incredibly easy, requiring no specialised skills or tools typically required in metal roofing projects. Naturally, you can expect easier installation and reduced project timelines.
- Lightweight: Unlike traditional metal roofs, standing seam profiles add minimal weight to the structure, making them ideal for retrofitting projects or buildings with weight constraints.
Ballasted Roof: Functionality in Any Application
Last, but certainly not least are ballasted roof finishes: the flexible solution that can be tailored to virtually any design-related or functional requirement. Using materials like gravel, paving slabs or rubber matting ensures your roof provides both protection and usability. Their versatility makes them highly popular in both residential and commercial settings. But how do they work?
It’s simple: ballasted roofs work by placing a layer of ballast – such as gravel or paving – over a roof’s waterproofing membrane. This has a multifunctional purpose, weighing down the membrane while providing a useful walking path for pedestrians. If you’re unsure whether a ballasted roof finish is the right choice, our list of benefits below will help:
- Customizable: Ballasted roofs can be customised to meet the specific needs of your roofing project. For example, gravel can be used for a simple and cost-effective finish, while paving slabs or pedestal systems can create functional walkways and outdoor spaces.
- Durable protection: The ballast layer protects the waterproofing membrane from physical damage and UV exposure, extending the lifespan of the roof you’re working on.
- Usability: Ballasted roofs are an excellent choice for projects that require usable outdoor spaces, such as terraces, balconies, or recreation areas. Rubber matting, for instance, provides a safe, non-slip surface ideal for schools, care homes or exercise areas.
- Efficient drainage: Pedestal systems used in ballasted roofs create free-draining spaces beneath paving slabs, preventing water pooling and ensuring efficient drainage.
- Sustainability:By incorporating recycled materials such as rubber mats, ballasted roofs can contribute to sustainability goals while delivering practical benefits.
Still Unsure? Speak to Our Roofing Experts
Still undecided on what choice of finish is right for your project? Don’t sweat it – your roofing partners at Tecron are here to help. For more information on any of the roof finishes mentioned in this guide, contact Tecron at technical@tecron.ie or call us on +353-91-353545. Alternatively, submit an enquiry via our Contact page. Let us help you create a roof that balances form, function and vision seamlessly.
How to Streamline Your Project with BMI Icopal Roofing Products
As a busy roofing contractor, you’ll understand better than anyone the importance of efficiency. From streamlining workflows to reducing the complexity of tasks, your roofing materials need to deliver on both of these objectives while minimising effort along the way. That’s why we’re pleased to highlight the game-changing technologies offered by BMI Icopal: now available from your nearest Tecron Trade Counter.
Costs are rising and deadlines remain tight. For many roofing contractors, saving time and costs while delivering outstanding results seems to be an impossible challenge. Fortunately, our partners at BMI Icopal have risen to the challenge with smart solutions that both eliminate unnecessary components and enhance existing systems. Here at Tecron, we’re proud to highlight their Torchsafe TA VCL Stripes and base layer systems as perfect examples.
BMI Icopal: Innovation Made Simple
Modern build requirements are becoming more and more complex and demanding. While roofing technology has generally evolved to meet these demands, our customers often find that these advancements typically require additional components, tools and adhesives. In many cases, these advancements can complicate – rather than simplify – their workflows. This is where BMI Icopal has come in.
BMI Icopal have made innovation simple by introducing groundbreaking products that simplify installation processes without sacrificing on quality or durability. For us, one standout innovation is the Torchsafe TA VCL Stripes system, which totally eliminates the need for separate adhesives when installing a fully-adhered warm roof buildup. This product reimagines the traditional Vapour Control Layer (VCL), turning it into a truly multifunctional component. Keep reading to learn more about this product, guaranteed to save on time and effort.
Torchsafe TA VCL Stripes: How the System Works
Torchsafe TA VCL Stripes represent the next generation of vapour control layers. But how? It’s simple: this system is designed to act as both a traditional VCL, as well as a thermally activated adhesive. This means that you can eliminate the need for additional glues or mechanical fasteners during the installation of an insulation layer, shaving chunks of time on your roof build-up process.
The system is installed in much the same way as any standard VCL in a torch-applied roofing system. For contractors, this means no extra tools or specialised equipment are needed – all you need is the standard torching equipment you’ll be used to using. Additionally, the VCL layer on Torchsafe TA VCL Stripes comes equipped with a top layer of thermally activated bitumen stripes. When heat is applied, the stripes bond directly to your insulation later, keeping it adhered securely to the roof deck, all without the need for traditional adhesives or fasteners. Who knew it could be so easy?
If you still haven’t made your mind up, the benefits we’ve listed below are sure to help. Let’s take a look at the advantages you can expect when using this exciting new product:
- Simplified installation: By removing the need for separate adhesives or mechanical fixings, the Torchsafe TA VCL Stripes system drastically simplifies the installation process. Contractors can use their existing torching equipment to carry out the entire installation, eliminating the hassle of managing multiple products and tools.
- Faster workflows: Because the same equipment is used throughout the process, the system allows for seamless workflows on busy roofing sites. This streamlined approach reduces installation times, enabling teams to complete projects faster while maintaining high standards of workmanship.
- Reduced material Costs: By combining the functions of a VCL and an adhesive, the Torchsafe TA VCL Stripes system reduces the need for additional materials, helping contractors cut costs without compromising quality.
- Improved safety: Fewer materials and less equipment mean fewer potential hazards on site. The reduced need for adhesives also eliminates exposure to potentially harmful chemicals, contributing to a safer working environment.
In-line with their commitment to innovation, BMI Icopal haven’t stopped with the VCL. They’ve applied the same stripes technology to the base later that sits on top of the insulation, serving as underlay for the cap sheet. Keep reading to learn more.
Tackling Build-Ups of Vapour & Condensation
By applying that same technology to the base layer, BMI Icopal have engineered an ingenious solution to two common issues in roofing: the build-up of vapour or condensation within the roof structure.
When adverse climatic conditions or installation timing result in vapour becoming trapped in the build-up, traditional systems often experience blistering: small pockets of trapped air or moisture that can compromise the roof’s integrity over time. Luckily for roofing contractors, BMI Icopal’s Stripes Technology solves this issue by allowing vapour to safely disperse underneath the cap sheet.
The strategic placement of stripes on the base layer is designed to release trapped vapour and condensation, eliminating the build-up of pressure. Aside from reducing the risk of blistering, this also ensures reliability and performance of your roofing system over time. Incorporating this technology into the base layer provides a range of significant benefits:
- Reduced blistering: Blistering is a common issue in roof build-ups, often leading to costly repairs and reduced system lifespan. The Stripes Technology significantly reduces the likelihood of blistering by providing a controlled way for vapour to escape, ensuring the roof remains durable and watertight.
- Enhanced system reliability: By mitigating vapour-related issues, the Stripes Technology enhances the overall reliability of the roofing system. Contractors can have confidence that the roof will perform as intended for its full lifespan, minimising the risk of callbacks or complaints.
- Cap sheet compatibility: The Stripes Technology base layer integrates seamlessly with BMI Icopal’s cap sheets, ensuring a smooth and efficient installation process from start to finish.
- Enhanced lifespan: By addressing vapour and condensation issues during the installation phase, the base layer technology contributes to a longer-lasting roofing system that can withstand the challenges of time and weather.
From simplified installation workflows to reduced material costs and enhanced system reliability, these solutions represent a significant step forward for the industry. Is your roofing supply keeping up?
*TorchSafe TA VCL Stripes is intended for use as an air & vapour control layer in a warm roof system build-up. Membranes should be installed in accordance with the manufacturer’s guidelines.
Tecron: Your Roofing Supply Partner
For more advice and detailed information on any of the above topics please contact us at Tecron where we will be happy to guide you though the variety of options available to you for your roofing applications. Here’s just a few ways to get in touch with us:
- Email: technical@tecron.ie
- Phone: +353-91-353545
Your Project, Our Passion
Reach out to Tecron today and discover how we can help you simplify your workflows, save on costs, and enhance the quality of your roofing projects with BMI Icopal.
8 Common Roofing Mistakes & How to Avoid Them
As a contractor, you get it: roofing is one of the most – if not the most – critical elements of any building. It protects the structure from the elements, provides insulation and plays a decisive role in energy efficiency. However, even the best-designed roof can fail if mistakes are made during the selection, installation or maintenance process.
As the person making those big decisions, you can be held at-fault if those errors lead to water ingress, energy efficiencies, structural damage or costly repairs. That means that it’s essential that you understand the most common roofing mistakes and how to avoid them. Look no further for the advice you need: this comprehensive learning resource contains everything you need to know. Thank us later!
Mistake #1: Choosing the Wrong Materials
The most common mistake we see being made? That’s easy: choosing the wrong materials. Every roofing project is unique, and selecting the wrong materials for a building’s specific requirements can be one of the most significant and costly mistakes you can make. Your choice of materials should carefully consider factors like climate, building design and budget.
Here’s an example. Lightweight, single ply membranes are a great choice for modern flat roof designs, while bitumen waterproofing is ideal for projects requiring traditional durability. Green roofs are a better choice for sustainability-minded projects, while EPDM is the go-to for long-term flat roof performance.
- Tecron Tip: Avoid the common roofing pitfall by discussing your requirements with one of our experts. We’ll use our decades of experience to ensure your choice is the right one. Simple!
Mistake #2: Not Installing Incorrectly
No matter the quality or performance of your materials, the entire system will often depend on the quality of installation. Poor sealing, insufficient adhesion, or gaps in coverage can allow water to penetrate the roof, leading to leaks and long-term structural damage. For example, failing to properly install liquid-applied waterproofing can leave unprotected gaps, while incorrect placement of insulation can create thermal bridging and reduce energy efficiency.
- Tecron Tip: Before getting to work, ensure you have the technical support and expert advice you need. Contact us to ensure you’re following manufacturer guidelines.
Mistake #3: Poor Ventilation
As any roofing contractor knows, poor ventilation often leads to the build-up of moisture and mould, as well as the potential rotting of structural materials. This is caused due to the formation of condensation, which is caused by warm air meeting cooler roof surfaces. When this moisture has nowhere to go, you can expect significant issues down the line.
- Tecron Tip: Using a Vapour Control Layer (VCL) is essential, alongside high-performance ventilation in your roof design. This will manage moisture effectively while enhancing the overall lifespan of your building. For more advice, check out our blog on this subject.
Mistake #4: Neglecting the Vapour Barrier
Time and time again, we point out the importance of a vapour barrier to ensure a successful roofing project. While some may install the vapour barrier incorrectly, others may forget to install it completely. Any mistake made in this area will cause your roof to be highly susceptible to water ingress and energy loss.
- Tecron Tip: Our advanced vapour control products are designed to integrate seamlessly into roofing systems as a reliable defense against moisture. Always remember to install the vapour barrier on the warm side of the insulation to maximise its effectiveness.
Mistake #5: Not Securing Your Materials During Installation
In the roofing industry, we love lightweight materials like insulation, membranes and vapour barriers. However, during strong winds, these nifty materials can quickly turn into dangerous projectiles, presenting a major risk to your health and safety – not to mention the safety of others at ground level.
- Tecron Tip: We recommend storing your materials at ground level until they’re ready to be installed. This is especially important during the winter season, when winds are typically a lot stronger. We recommend using a decent fastening system to ensure your components are held firmly in place during unpredictable weather.
Mistake #6: Not Paying Attention to Drainage
Drainage is a critically important consideration for virtually any flat roof design. If a drainage system isn’t designed or installed correctly, you face an increased risk of water pooling. This will inevitably add extra weight to the roof and increase the risk of leaks, structural damage and total failure. As a roofing contractor, this is the last thing you’ll want to deal with.
- Tecron Tip: We recommend planning your drainage systems with care and attention to detail, incorporating adequate slopes, outlets and channels. For advice on reliable outlets and accessories, contact us today.
Mistake #7: Neglecting Night Seals and Disregarding Weather
We’ve already talked about the importance of keeping your materials tied down and secured during periods of windy weather. However, that’s not the only environmental condition you should be wary of. By neglecting to install temporary seals over work-in-progress roof areas, you risk causing potential damage to insulation and other materials. Aside from that, disregarding weather conditions can cause major issues, with rain, high winds and extreme cold threatening to compromise your adhesion, damage your materials and create unsafe working conditions.
- Tecron Tip: Always install night seals to protect unfinished sections of your roof (EPDM Flashing Tapes are a great solution). As far as unpredictable weather goes, we advise planning your roofing project around favourable weather forecasts, ensuring you arrive on-site fully equipped with protective tarps or covers to shield work-in-progress areas from sudden changes.
Mistake #8: Skipping Regular Maintenance
Last but not least, let’s take a look at one of the most common roofing mistakes we see: neglecting regular maintenance. Once a roof is installed, it’s easy to assume that the work is done. However, skipping regular maintenance can allow small issues—such as clogged drains or minor wear—to turn into major problems over time.
- Tecron Tip: Schedule routine inspections to check for signs of wear, leaks or debris. Tecron’s experts can provide guidance on ongoing roof care and suggest products to help prolong the life of your system.
Avoid Roofing Errors: Partner with the Pros
As with an area of specialised work, accidents do happen. However, by partnering with a true expert that’s always on-hand to provide the advice you need, you can keep these potentially costly errors to a minimum. To learn more about how we can help, check out the section below.
Ensure Reliable, Consistent Results with Tecron
Regardless of your project’s unique requirements or the challenges you face, we’ve got the experience, expertise and inventory to help. To reach out to one of our roofing experts now, simply reach out with your query to info@tecron.ie. Alternatively, call us on 0818 75 75 75 (or +353 91 353 545 outside of RoI), or visit our Trade Counter.
The Contractor’s Guide to Winterproofing Projects
With the dark evenings drawing in, the chill of winter has officially arrived. For roofing contractors across the UK and Ireland, ensuring buildings are properly winterproofed is at the top of the agenda. In the latest learning resource from Tecron, we explore some key considerations and actionable tips you can follow to ensure your roofing systems are ready for winter.
The winter seasons seem to become more challenging every year, with weather events like heavy rainfall and high winds presenting a significant challenge to both commercial and residential roofs. Now more than ever, winterproofing is essential not only for safeguarding the structural integrity of a building, but also the safety of workers and residents.
Why is winterproofing so important?
We all know that winter weather can be unpredictable and unforgiving. However, statements by the Environmental Protection Agency (EPA) highlight that this problem is to get worse in future years, with the number of intense storm periods set to increase along with levels of heavy rainfall. Roof areas in particular are highly vulnerable during construction or repair work, with lightweight materials like insulation and waterproofing membranes potentially becoming dangerous projectiles if not properly secured.
Aside from that, improperly prepared roofs will become more susceptible to water ingress, leading to damage not only to materials, but also the building’s interior. Fortunately, there are a number of steps that contractors can take to prevent damage that could otherwise lead to costly delays, repairs and for building owners across the board, the time to act is now. For steps you can take to winterproof your roofing project, keep reading.
A Guide to Winterproofing Your Roof
Winter presents many challenges. However, there are many steps you can take to mitigate these challenges, from basic safety steps like avoiding the overstacking of products to more considered approaches such as planning for day-by-day installation. Let’s take a closer look.
How to Winterproof Your Project
- Avoid overstacking: This is one of the most common mistakes we see being made in roofing projects, and presents major risks during more extreme weather conditions. While it may seem efficient to place everything on-site at once, it really drives up the risk of materials being blown away in high winds, turning them into potentially dangerous projectiles. Our tip here is to store materials at ground level wherever possible, only bringing them to roof level in manageable quantities when needed. Aside from reducing the risk of wind damage, this also generally improves on-site organisation and safety.
- Use night seals: Unfinished roof areas are especially vulnerable to water ingress during winter. Night seals provide temporary protection, preventing rainwater from seeping into exposed sections of the roof or insulation layers. Our advice is to use Tecron Self-Adhesive EPDM Flashing Tapes for night seals. These tapes are designed to form a reliable barrier, keeping water out and safeguarding work-in-progress areas until construction resumes.
- Cover and secure uninstalled materials: As a roofing contractor, you’ll understand that materials can degrade quickly when exposed to the elements, causing them to lose their structural integrity or waterproofing capabilities. This is why we recommend that you always securely cover any uninstalled materials with tarpaulins or other weatherproof coverings. For peace of mind, we advise that you weigh these down, or tie them to prevent them being displaced by the wind.
- One day at a time: For higher levels of safety, it’s worth planning your work incrementally. You should only expose or open as much of the roof as can be covered or completed within the same day. Installing insulation in manageable sections ensures each area is fully covered with waterproofing layers before moving on. We also advise that you avoid leaving insulation exposed overnight or during rainfall, as water can pool on the vapour barrier and compromise its effectiveness.
- Fully adhere materials wherever possible: Fully adhering roofing membranes and insulation provides greater resistance to water ingress during work-in-progress stages. It creates a stronger bond, minimising the risk of materials lifting or becoming dislodged during adverse weather conditions. When fully adhering membranes or insulation, Tecron recommends using high-quality products specifically designed for winter applications to ensure durability and long-term performance.
- Account for vapour & water management: Last but not least, let’s talk about vapour and water management, one of the less visible but equally critical elements of winterproofing. Always remember that water ingress does not only occur from rain, but also from condensation caused by fluctuations in temperature. By incorporating vapour control layers into your roofing system, you can prevent moisture build-up in the roof structure. When combined with proper insulation and ventilation, you can manage temperature fluctuations effectively.
4 Advantages of Proactive Winterproofing
By taking these steps to winterproof your roof, you’re not only protecting materials and structures but also setting your project up for success. Here are some of the key benefits:
- Reduced delays & costs: Weather-related damage can result in costly repairs and delays that throw off project timelines. Proper winterproofing minimises these risks, ensuring smoother progress and fewer unexpected expenses.
- Improved safety: Winterproofing reduces the likelihood of accidents caused by unsecured materials or water ingress. This is especially critical for ensuring compliance with health and safety standards.
- Long-term durability: Roofs that are properly prepared for winter weather are more likely to stand the test of time. Protecting materials and ensuring correct installation processes result in a stronger, more durable roofing system.
- Peace of mind: Whether you’re a contractor or a building owner, knowing that your roof is protected against the harshest conditions provides valuable peace of mind during the unpredictable winter months.
Tecron: Winterproofing Your Next Project
Need more advice on how you can take steps to winterproof your next roofing project? Don’t sweat it. Our experts are on-standby to answer any queries you have. To get started, browse some of the products we have on offer. Alternatively, reach out to sales@tecron.ie , call us on +353-91-353545 or submit a query through our dedicated contact page. Let’s get started!
Tecron Achieves ISO Certification
In the fast-paced, competitive construction market, adhering to internationally recognised standards is no longer a luxury: it’s a necessity. That’s why we’re delighted to announce that we’ve achieved ISO Certification for Quality Management (ISO 9001), Environmental Management (ISO 14001), and Occupational Health & Safety Management (ISO 45001), demonstrating our continued commitment to transparency, accountability and best industry practices.
For all of us at Tecron, this milestone reflects our unwavering commitment to operating at the highest standards, not only for our customers, but also for our employees, our suppliers and our natural world. But what does ISO Certification mean, and why does it matter?
What is ISO Certification?
ISO (International Organisation for Standardisation) Certifications are recognised around the world, and guide organisations like ours in achieving operational excellence. These certifications provide a structured approach to managing quality, sustainability and safety, helping us to align what we do with international best practices. For us, securing this certification is the result of lots of hard work, dedication and a commitment to doing right by you.
So – what does it mean for you, our suppliers and our many stakeholders? First and foremost, our ISO Certification is a badge of trust and reliability. It is genuine proof that we’re serious about delivering consistent results for our customers, reducing environmental impact and ensuring the wellbeing of our workforce along the way. For us, this isn’t just a compliance exercise – it’s a serious statement that underlines our commitment to improvement, transparency and leadership in our industry.
ISO 9001: Delivering Consistent Quality
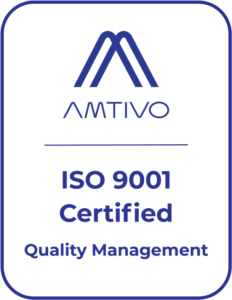
With our attainment of ISO 9001 Certification, we demonstrate our ability to deliver high-quality products and services that exceed your expectations. It provides us with a genuine framework to achieve this consistently thanks to a robust Quality Management System (QMS). With this new certification, we’ve achieved the following:
- Established clear, documented processes for all operational activities.
- Enhanced leadership and decision-making based on evidence and data.
- Built a culture of continuous improvement, ensuring we’re always evolving to meet the needs of our customers and the market.
As a Tecron customer, you can trust that each one of our products meets the highest standards of excellence in roofing solutions.
ISO 14001: Pioneering Sustainability
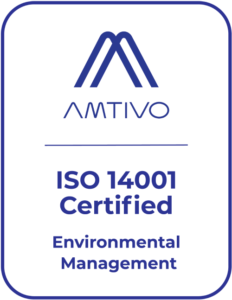
We’re passionate about building sustainable practices into everything we do. With ISO 140001 Environmental Management Systems (EMS) Certification, we’re now proud to demonstrate our commitment to environmental stewardship. With ISO 14001 Certification, we have:
- Implemented systems to manage and reduce our environmental footprint.
- Ensured compliance with all relevant environmental regulations.
- Created opportunities for innovation in sustainable roofing materials and practices.
With this new certification, our customers can now partner with a company who can demonstrate that sustainability and performance can go hand-in-hand.
ISO 45001: Protecting Our People
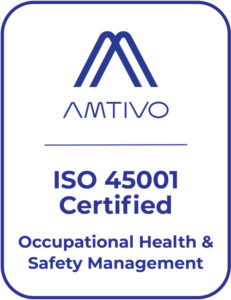
Our commitment to excellence goes far beyond our dedication to our customers and the natural world. Our greatest asset is our people, and ISO 45001 Occupational Health & Safety Management Certification puts a stamp on our commitment to creating a safe and supportive working environment for everyone. With ISO 45001 Certification, we ensure that we:
- Actively identify and manage workplace risks.
- Provide training and resources to enhance employee safety.
- Foster a culture of accountability and continuous improvement in health and safety practices.
By achieving ISO 45001, Tecron has taken proactive steps to minimize workplace incidents and create a safer, more productive environment for everyone.
Why Should You Care?
This is a fantastic milestone for us – but what does it mean for you? It’s simple:
- Quality you can rely on: Every product and service we deliver is backed by rigorous quality control processes.
- Sustainable solutions: Our commitment to environmental responsibility extends to the materials we supply and the partnerships we build.
- Safe practices: From our team to yours, safety is embedded in everything we do.
When you work with Tecron, you’re not just getting exceptional products—you’re partnering with a company that is fully committed to quality, sustainability, and safety at every step of the journey.
Looking to the Future
As we look to the future, our commitment to improvement with ISO Certifications has only just begun. This milestone provides us with a new and exciting foundation for continuous improvement. We will continue to push the boundaries of innovation, refining our processes and finding new ways to better serve you: our valued customer.
We’d like to take this opportunity to send a massive thank you to everyone in our team for their hard work in helping us achieve this milestone. It is their dedication to the highest standards that have helped us get to where we are today. This goes out to you!
Discover the Tecron Difference
Our ISO certification is a testament to our commitment to excellence, and we’re excited to bring that same level of dedication to your next project. To find out what we have on offer, check out some of the products we have in-stock by visiting our website. Alternatively, call us on + 353 91 353 545, email us at sales@tecron.ie or simply visit our Trade Counter to avail of our expert advice.
Why Choose Liquid Waterproofing? A Guide for Roofing Contractors
Among the many innovations seen in roofing technology over recent years, liquid waterproofing has seen some of the highest levels growth and development, evolving from a niche solution into one of the most trusted and versatile methods for flat roof coverings and waterproofing. From its flexibility and durability to ease of installation, we explore why liquid waterproofing has cemented its place as a top choice for professionals in the roofing industry.
The advantages of liquid waterproofing are broad ranging, secured by nearly four decades of research, development and real-world application. Now, we see a selection of products that have been developed to the highest performance standards, backed up with best-in-class technical expertise. This combination of factors means that liquid waterproofing can be incorporated into full Built-Up Roofing (BUR) applications, whether that’s for new builds, refurbishments or as an upgrade method for existing substrates.
At Tecron, we believe that the advent of high-performance waterproofing in a liquid form has arrived, and it truly has to be seen to be believed. Let’s take a closer look at how this evolution has made liquid waterproofing one of the most viable and popular options for flat roofs and other waterproofing needs.
Why Do Contractors Choose Liquid Waterproofing?
Today, liquid waterproofing solutions are a far cry from their early iterations, boasting state-of-the-art formulations that provide users with unmatched performance and ease of use. The continuous investment in research and development has resulted in products that are not only more stable but also highly adaptable to varying conditions.
Whether it’s blistering heat, pouring rain, or freezing temperatures, modern liquid waterproofing systems are designed to perform under virtually any environmental circumstance. Below, we delve into the details. Keep reading to learn more.
Essential Considerations for Roof Design & Preparation
Several considerations directly impact the overall functionality, durability and compliance of your roof with local building regulations. Let’s take a closer look at each of these considerations, starting with u-value requirements.
1. Ease of Application
A key benefit of liquid waterproofing is in the ease of installation it provides to roofing contractors. While traditional waterproofing methods typically require the use of heat or complex installations, liquid systems are applied cold, directly from the container. This offers two major advantages: it eliminates the need for heavy machinery or specialist tools, and also makes the application significantly faster and safer.
Beyond that, it’s important to note that liquid waterproofing can be applied to an incredibly wide range of substrates, from concrete and timber to asphalt and metal. The adaptability liquid waterproofing provides makes it a versatile solution for use on new construction projects as well as refurbishments on older structures.
From our experience working with contractors across the UK and Ireland, the ability to quickly and efficiently apply liquid waterproofing – especially in challenging weather conditions – significantly reduces labour costs and project timelines.
2. Seamless, Fully Integrated Finish
As a roofing contractor, you will work with clients who demand the highest quality of finish on their building. Few other solutions provide a finish as seamless as liquid applied solutions.
Unlike membrane-based systems that typically rely on joints and seams, liquid waterproofing creates its own, fully integrated membrane that effectively eliminates weak points that would otherwise be susceptible to the penetration of water. This results in a continuous, joint-free surface that lowers the risk of leaks, guaranteeing long-term protection for roofs and other surfaces.
Another key benefit of the liquid nature of this solution is in how it can be easily moulded around more intricate details, penetrations or awkward roof shapes: scenarios where traditional materials tend to struggle. This makes liquid waterproofing ideal in situations where you’re working on a complex roof design with installations such as skylights or HVAC units.
3. Durability & Flexibility
Liquid waterproofing is engineered with longevity as a top priority. Of course, this is essential where buildings may be susceptible to thermal expansion and contraction. Roof surfaces tend to expand and contract as temperatures fluctuate, causing traditional materials to crack or become brittle over time.
With liquid waterproofing, these concerns are eliminated. This is because liquid waterproofing’s elasticity allows it to move with the building while simultaneously maintaining its watertight seal. That means the waterproofing later remains intact, even when the building is subject to extreme temperature variations.
4. Rapid Cure Technology
On virtually any construction project, time is of the essence. This is especially true across the UK and Ireland, where contractors are often working on projects that are weather-dependent. Thanks to the incorporation of rapid cure technology, liquid waterproofing is quickly set after application, ensuring the roof is watertight almost immediately. The result? Faster project completion and reduced downtime.
5. Accreditations and Standards
Today’s construction industry demands proof of the most rigorous approaches to testing and accreditation, and liquid waterproofing has gained industry-wide trust in this area. The leading manufacturers who engineer liquid waterproofing systems ensure their products meet the highest performance standards, backed by key certifications from FM, BBA and ETA.
For contractors, these accreditations are critical. They provide specifiers and contractors with priceless peace of mind that they have chosen a product that has been thoroughly tested and guaranteed to perform in a wide variety of conditions.
6. Ease of Maintenance and Repair
Regardless of how advanced it is, the fact is that no waterproofing system is completely immune to wear, tear or accidental damage. Despite this, it is important to consider that liquid waterproofing systems are significantly easier to repair compared to traditional materials.
If a section of the roof becomes damaged by foreign objects or excessive wear, the affected area can be easily repaired without the need to remove large sections of the waterproofing layer. Aside from saving time and money on your project, it also ensures that the building will remain protected from potential water ingress.
Liquid Waterproofing: Other Advantages to Consider
The factors listed above only provide a brief overview of the benefits offered by liquid waterproofing systems. Beyond those factors, liquid waterproofing offers its own benefits when it comes to general versatility, as well as sustainability.
- General versatility: Whether you’re working on a high-traffic roof that needs reinforced walkways or a more decorative finish, liquid systems allow for the easy incorporation of various design elements. Non-slip surfaces, vibrantly coloured walkways, and other markings can be added using a single product, making it an all-in-one solution for various aesthetic and functional requirements.
- Sustainability benefits: As the construction industry moves toward more sustainable practices, liquid waterproofing systems are proving to be a greener option. Many of these systems are low in volatile organic compounds (VOCs) and free from harmful chemicals, making them safer for both installers and the environment. Additionally, the long lifespan of liquid waterproofing systems means fewer replacements, which translates to less waste over the building’s life cycle.
If you’re considering liquid waterproofing for your next project, we invite you to explore our range of products, backed by best-in-class warranties and support.
Tecron: Your Project, Our Passion
At Tecron, we pride ourselves on offering high-performance liquid waterproofing systems that meet the demands of modern construction. To upgrade your supply, begin by browsing our full selection of liquid waterproofing systems. Alternatively, reach out to one of our experts today to discuss your unique project requirements.
Roof Design & Preparation: A Guide for Modern Construction
In today’s fast-changing construction sector, the demand for sustainable, energy-efficient and aesthetically pleasing buildings has never been higher. But why have roof design and preparation become so critical in meeting these objectives? In a comprehensive learning resource from Tecron, we explore the critical aspects of roof design and preparation, outlining the key components that contribute to a high-performing, long-lasting and aesthetically pleasing roof.
Whether you’re working on a new build or a retrofit project, a well-designed roof isn’t just desirable: it’s essential. Adhering to key design principles is of the highest importance when it comes to not only protecting a building, but also in terms of meeting energy efficiency standards and ensuring the overall comfort of its occupants.
Here at Tecron, we believe that a detailed and thoughtful approach to roof design can be achieved by engaging with our clients and their design teams from the earliest opportunity, allowing our roofing experts to guide and direct the requirements of your package to ensure successful project outcomes.
Roof Design & Preparation: The Importance of Early Engagement
There are many factors to consider to ensure a successful roof installation, but few are as important as ensuring early engagement between roofing professionals and the client’s design team. By having these discussions early on in the process, we help our customers scope out the specifics of their roofing package. While this helps avoid costly design changes or unexpected issues later in the project, it also allows us to to assess some critical factors which we’ve listed below:
- U-values: Getting a full understanding of u-values, we can determine the necessary thermal performance of the roof.
- Insulation methods: Early engagement ensures that our team can identify the best approach to insulation from both a performance and installation perspective.
- Condensation risk analysis: Our experts specify a roof system that mitigates condensation risks and prevents moisture build-up that could potentially lead to structural damage.
- Roof junctions: We can quickly address cold bridging issues at roof junctions to improve the overall energy efficiency of the building you’re working on.
- Wind-load calculations: Through early engagement with clients and their design teams, you can proceed in confidence that the roof can withstand local wind conditions.
- Deck type consideration: Tecron’s expert team can identify the best roofing solutions based on the type of deck being used, whether that’s concrete, timber or metal.
Aside from those key considerations above, early engagement also helps inform your decision making based on any required guarantee periods, as well as the roof finish in question (eg. green roofs, fully adhered systems, mechanically fastened, paved, decked or standing steam profiles). In the next section, we look at each of these considerations in detail, and what they mean for your project.
Essential Considerations for Roof Design & Preparation
Several considerations directly impact the overall functionality, durability and compliance of your roof with local building regulations. Let’s take a closer look at each of these considerations, starting with u-value requirements.
1. U-Value Requirements
Put simply the U-Value of a roof refers to its thermal performance and how well it can retain heat within the building. U-Values that are lower typically indicate better insulation performance: a crucial aspect in reducing energy consumption and improving the overall comfort of a building. By understanding U-Value, you can make an informed decision on the best insulation materials and methods.
2. Insulation Methods
Proper roof insulation requires a combination of the right materials and methods. Tecron’s advice in this area will depend on the general performance of the roof and its installation complexity, as well as your available budget. Below, we’ve listed three of the most common insulation options available:
- Warm Roof: Insulation placed above the roof deck, providing a continuous thermal envelope. This is an effective method for preventing cold bridging.
- Cold Roof: Insulation placed below the roof deck, which can create ventilation challenges but may be more suitable for certain designs.
- Hybrid Roof: A combination of warm and cold roof techniques, which may be used in specific cases to enhance performance.
3. Condensation Risk Analysis
As discussed in some of our previous learning resources, condensation can become a significant issue in roofing systems if not properly managed. When warm, moist air from the building meets cold surfaces on the roof, that quickly condenses into water. In-turn, this can lead to the growth of mould which can lead to severe structural damage and degradation to your insulation system.
Fortunately, Tecron conducts condensation risk analysis to ensure your design and material selection prevents moisture build up. This is an area where proper ventilation, vapour barriers and insulation methods are critical.
4. Junctions & Cold Bridging
Cold bridging happens when heat escapes through structural elements that are poorly insulated compared to surrounding areas, most commonly roof junctions. Aside from leading to condensation, this can also cause significant energy deficiencies and lower levels of comfort for building occupants. To minimise this risk, we ensure that roof junctions are optimised, with insulation addressing weaker points in the building.
This is another area where early engagement is key. Proper attention to detail during the design phase can significantly improve the energy efficiency of the building and reduce heating and cooling costs.
5. Wind-Load Calculations
Any roof must be properly designed to calculate wind loads expected in its location. Put simply, this ensures the roof system is strong enough to resist wind uplift and prevent potential damage during adverse weather conditions. Wind load calculations consider a number of factors ranging from building height and location to wind exposure, ensuring the roof remains structurally sound.
6. Deck Type Considerations
The type of deck used in a roof structure—whether concrete, timber, or metal—has a significant impact on the overall roof design. Each material presents unique challenges and opportunities:
- Concrete decks: These are typically strong and durable but may require additional waterproofing measures.
- Timber decks: Timber decks are lightweight but may require careful consideration of moisture control to prevent rot.
- Metal decks: Metal decks are durable and quick to install, but they require insulation and vapour barriers to prevent condensation.
Understanding the deck type early in the design process allows Tecron to recommend the best waterproofing systems and insulation methods for optimal performance.
The Importance of Skilled Installers and Technical Support
As we conclude this learning resource, we’d like to remind our customers that a well-designed roof is only as good as its installation. By ensuring that the roofing system is applied by trained and accredited installers, you can ensure that it provides the performance and longevity required. Here at Tecron, we place a strong emphasis on technical support throughout the installation process, offering:
- On-site inspections: Regular inspections during installation to ensure compliance with specifications and warranty requirements.
- Material and warranty compliance: Ensuring that the installation meets the standards required for material warranties and additional insurance-backed warranties requested by the client.
- Ongoing technical support: Providing technical assistance throughout the project to address any challenges that may arise.
Tecron: Your Project, Our Passion
For the most up-to-date and relevant information on your specific roofing needs, contact the Tecron team early in the project lifecycle. Our experienced professionals are here to guide you through the process, ensuring that your roof performs at the highest standards for years to come. Reach out today or email us directly sales@tecron.ie.
How to Reduce Costs with a Tube & Screw Fixing Combo
If you’re a roofing contractor constantly dealing with requests to improve thermal performance and the overall efficiency of a building, there are plenty of options to choose from. However, your customers might gasp at some of the hefty price tags that come along with these objectives. That’s why we’re revealing one innovation that manages to enhance performance while keeping costs in check: our favourite thermally broken fixing: the plastic tube and screw combination.
Thermal performance is a top demand in modern construction, and it’s not hard to see why. Insulation thicknesses are gradually increasing in order to maintain consistent indoor temperatures all-year-round. The way that these materials are attached forms a critical aspect of the building’s overall performance. where the attachment methods are inadequate, the users of that building can expect thermal bridging as a consequence, compromising the effectiveness of their insulation and sending energy costs skyrocketing.
So, how does thermal bridging happen in the first place? While there are many causes, it is important to know the role that traditional metal fixings can play in this scenario. Heat is conducted through the metal, which bypasses the insulation. The result? Significant energy losses and uneven temperatures throughout the building. The fact is that any solution you’re looking for should seek to eliminate the chance of this happening.
The Tube & Screw Combo Explained
If you’re looking for a solution that doesn’t break the bank, the plastic tube and screw combination is a top contender. This solution is designed to eliminate direct contact between the fixing screw and the external surface temperature.
Tube & Screw Combo: How It Works
This combination is the definition of simplicity and effectiveness. It all works by dropping the fixing into a plastic tube, which greatly reduces – and even eliminates – thermal bridging. For example, if using 200mm thick insulation, a plastic tube of 185mm in length is employed, and a fixing length of just 60mm is sufficient to secure the insulation to the deck or membrane.
The Tube & Screw combo is also one of the most versatile and adaptable options you’ll find. Indeed, the Eurofast fixing range offers various diameters of heads on the tubes, making them adaptable to virtually any application. Investing in this level of flexibility ensures that the system can be used in a broad range of building scenarios, providing a robust and highly versatile solution for thermal performance enhancement.
The Benefits of the Tube & Screw Combo
Aside from its raw effectiveness, adaptability and versatility, opting for the tube & screw combination offers a variety of benefits. We’ve highlighted some of those key benefits below, ranging from ergonomics & installer welfare to the technical support you can expect. Keep reading to learn more:
Reduced costs: By using this neat combination, you can cut fixing costs by up to half compared to traditional metal plate and long fixing screws. This makes the combo an attractive choice for budget-conscious projects without sacrificing on performance.
Reliable performance: It doesn’t just save on money, it saves on time. There is no drop in the holding capacity of the tube & screw combo, and provides reliable, secure attachment of insulation materials.
Ergonomics as a priority: Another advantage of the Tube and Screw combo is the reduction in the overall weight of the fixings used. This makes the system more ergonomic, reducing the physical strain on installers and enhancing their welfare on site. Meanwhile, the tube & screw combo can be installed quickly and efficiently (the availability of preassembled Tube and Screw combos and fully automated installation tools further streamlines the process, making it a preferred choice for many installers).
Technical support & services: Accurate wind-load calculations are essential for ensuring the stability and safety of any roofing system. Eurofast provides wind-load calculations specifically tailored for the Tube and Screw system, ensuring that each installation meets the necessary safety standards. Aside from that, Eurofast offers preassembled Tube and Screw combos. This reduces on-site preparation time, allowing installers to focus on securing the insulation materials quickly and efficiently.
The Environmental and Long-Term Benefits
There’s more benefits to the tube & screw combination other than the advantages it provides around cost-savings and performance. There are also major sustainability benefits to be considered here.
The reduction in thermal bridging and improved energy efficiency contribute to a building’s overall sustainability. By minimising energy losses, the Tube and Screw system helps reduce the building’s carbon footprint, aligning with modern sustainability goals. This is combined with the fact that the materials used in the Tube and Screw system are designed for long-term durability. The plastic tubes are resistant to corrosion, unlike traditional metal fixings, which can degrade over time. This longevity ensures that the system continues to perform effectively throughout the building’s lifecycle.
Tecron: Your Roofing Supply Partner
To find out how Tecron can help with your next project, please contact the Tecron team today by emailing sales@tecron.ie or call us on +353-91-353545. Alternatively, visit one of our Trade Counter to avail of our industry expertise in-person.
Understanding the Importance of Proper Ventilation
Few industries enjoy the level of innovation as seen in the world of building technology, with advancements such as air handling systems, solar power integration and air-to-water heating systems transforming the sector. Indeed, with all of these innovations, you may be mistaken in believing that ventilation has taken a back seat. In a learning resource from Tecron, we debunk this myth, highlighting that ventilation is just as important as ever.
Building technologies have evolved significantly over recent years, and it’s not hard to see why. Throughout Ireland and the UK, governments and local authorities have joined in a quest to enhance energy efficiency and thermal performance across the grid. This is only part of the reason why we’ve seen modern buildings undergo such a surge in terms of embracing new technologies that reduce energy consumption.
Whilst this move towards more sustainable processes should be welcomed, it should be approached with full knowledge of the new challenges they present – particularly in regards to ventilation. Many contractors will understand that as buildings become more airight to improve energy efficiency, the risk of inadequate ventilation increases. When not addressed, this can lead to major issues around moisture and air quality.
The reasons for these potential issues are numerous. However, it is generally understood that highly insulated and airtight structures can create pressure points, particularly in roof areas and junctions between roofs and walls. Managing these pressure points and ensuring that a building performs optimally throughout its lifecycle is critical, and can only be truly achieved through proper ventilation methods. Your choice of method will largely depend on the type of roof build-up you’re working with, which we’ll get onto in the next section.
Types of Roof Build-Ups: An Overview
Before deciding on how to approach ventilation in any building, it is important that contractors first understand the type of roof build-up they’re working with. There are primarily three types of roof constructions you should be aware of: warm roof, cold roof and hybrid roof. Let’s take a look at these build-ups and what they may require in terms of ventilation:
- Warm roof: In a warm roof build-up, all the insulation is placed on the outside of the roof deck, and the insulation is laid directly onto a vapour barrier. This method ensures that the roof deck and all structural elements are kept warm, which helps to prevent condensation within the structure.
- Cold roof: In contrast, a cold roof build-up involves placing the insulation on the underside of the decking. This method must be ventilated, making it crucial to understand how to properly manage airflow to avoid condensation and cold bridging.
- Hybrid roof: A hybrid roof combines elements of both warm and cold roof constructions, with insulation placed both under the deck and on top of it. This method requires specialist vapour barriers and precise installation to function correctly.
Roof Ventilation: Key Considerations for Contractors
Understanding the type of roof build-up you’re working with is only one of the considerations you must make before deciding on your approach to ventilation. Below, we’ve listed some of those other key considerations, ranging from roof pitch to the potential need for vapour barriers. Take a read and stay informed:
- Roof pitch: In order to ensure proper ventilation, it is essential that the pitch of the roof is greater than 12 degrees. This is because steeper roofs allow improved airflow and a reduced risk of dead zones.
- Flat roof construction: If you’re working on a flat roof, it should ideally be constructed as a warm roof wherever possible. Taking this step will prevent many of the ventilation issues associated with cold roofs (if you’re unsure about what these issues are, reach out to Tecron and we’ll be glad to help).
- Cold roof width: In all cases, contractors should avoid constructing cold roofs with a width greater than 5 metres. This is because airflow can become stagnant in the middle of the roof, leading to an increased risk of moisture-related issues.
- Warm roof ventilation: Take our advice – never attempt to ventilate under a warm roof construction. This will only lead to reduced effectiveness in the insulation, leading to more costs for your customers to bear.
- Insulation wrapping: In warm roof constructions, aim to wrap the insulation completely around the structure. For example, on a flat roof with soffit overhang, insulate the fascia and soffit to prevent cold bridging of timber, steel, or concrete decks.
- Vapour barriers: Last, but not least, it’s important to think about the importance of vapour barriers. It is necessary to install a vapour barrier on the warm side of the insulation (even in cold roof constructions), inside the building or draped between joists to reduce moisture and prevent condensation from getting a foothold.
Understanding the Impacts of Poor Ventilation
Decades of experience in the roofing industry has taught us a thing or two about the real consequences of approaching ventilation in the wrong way. The results can be catastrophic. Here’s just a few of the consequences you can expect:
- Condensation damage: The condensation of moist air on cold surfaces can lead to water damage, mould growth and even structural deterioration.
- Cold bridging: Poor ventilation often leads to cold bridging, where heat escapes through the building envelope. The result? Reduced energy efficiency and more condensation.
- Roof failure: In a worst case scenario, poor ventilation can eventually lead to the total failure of a roof. This naturally results in costly repairs and structural damage – not to mention the potential health threats posed by mould & dampness.
Best Practices for Roof Ventilation
There are four essential steps that can be taken to avoid the pitfalls of poor air circulation. See below:
- Proper design consideration: During the design phase, plan for adequate ventilation by incorporating vents, breathable membranes and ensuring sufficient airflow.
- Conduct regular inspections: Conduct regular inspections of the roof and ventilation systems to identify and address any issues promptly.
- Ensure professional installation: Ensure that ventilation systems are installed by qualified professionals who understand the complexities of modern building technologies.
- Ensure regular maintenance: Regularly maintain and clean ventilation systems to ensure they function correctly and efficiently.
Ensure you follow these best practices, and ensure you and your team are aware of the dangers of poor ventilation by sharing this blog with your colleagues. For more information on this issue, simply reach out and we’ll be glad to help.
Tecron: Your Roofing Supply Partner
To find out how Tecron can help with your next project, please contact the Tecron team today by emailing sales@tecron.ie or call us on +353-91-353545. Alternatively, visit one of our Trade Counter to avail of our industry expertise in-person.
The Importance of Pull-Out Tests and Fixing Patterns for Flat Roofing Projects
Unlike any other construction work, flat roofing projects come with a raft of unique challenges that demand the highest levels of planning to ensure structural integrity, durability and long-term performance. Pull-out tests are one of the most important elements of this process, establishing appropriate fixing patterns and more. In the latest learning resource from Tecron, we highlight everything roofing contractors need to know about pull-out testing.
Pull-Out Testing: An Essential Process
From verifying fixing strength and space optimisation to assessing substrate integrity and mitigating wind uplift risks, pull-out testing ensures comprehensive insights that ensure optimum end results. We’ve identified six key areas that make pull-out testing a bare essential on your flat roofing project. Keep reading to learn more…
1. Verify Your Fixing Strength
One of the core benefits of pull-out testing is that they provide accurate empirical data on the strength of the fixings used in your flat roof installation project.
Pull-out testing simulates real-world conditions and assesses your fasteners’ ability to withstand load-bearing requirements by subjecting them to controlled tension forces. By verifying your fixing strength, you can ensure that your choice of fixing pattern can sufficiently secure roofing membranes, insulation layers and other components. The end result? A finished project that minimises the risk of structural failures or material detachment.
2. Optimise Your Fixing Space & Layout
There are a number of factors that effective fixing patterns depend on, ranging from roofing materials and substrate conditions to climate and building usage.
Fortunately, pull-out testing allows engineers and contractors to use empirical evidence to fully justify their fixing spacing and layout, as opposed to relying on manufacturer recommendations or theoretical calculations. This process allows you to systematically test a variety of configurations, including different spacings and orientations.
More than any other planning process, pull-out testing helps identify the most efficient and robust fixing pattern for your flat roofing project.
3. Assess the Integrity of Your Substrate
Your flat roof substrate will largely vary in its composition and condition, weather that’s concrete, metal decks or timber structures. By conducting thorough pull-out testing, engineers and contractors can both evaluate the performance of their fixings whilst also receiving data-informed insights into the integrity of the underlying substrate.
This is a significant benefit as detecting weaknesses or inconsistencies in the substrate provides space for remedial measures to be implemented, ensuring a strong and stable foundation for grounding the roofing system.
4. Mitigate the Risks of Wind Uplift
Wind uplift presents a significant threat to flat roofing, especially in Ireland where strong winds are a common weather characteristic. Pull-out testing is one of the most comprehensive ways of assessing your fixings’ resistance to wind uplift forces, guiding design and installation teams in determining the best fixing patterns and specifications.
By determining this information, you can contribute to the overall resilience of your flat roof against wind-related damage or failure.
5. Ensure Quality Assurance and Compliance
Where quality assurance protocols are concerned, pull-out testing processes are a bare essential. This is because these tests objectively evaluate the performance of your fixings; ensuring compliance with industry standards, building codes and project specifications.
By providing full documentation of your tests, you can provide your stakeholders with the confidence they expect in the reliability and safety of your completed project, fostering accountability and transparency throughout the construction process.
6. Predict Long-Term Performance
Roofing contractors will understand that the durability and longevity of their flat roofing system will hinge on the effectiveness of their fixings in maintaining structural integrity over a period of time. Only by conducting comprehensive pull-out tests contractors can predict long-term performance and proactively identify any issues that may arise across the lifespan of the roof.
By proactively addressing fixings-related concerns based on pull-out test results, stakeholders can mitigate maintenance requirements, minimize lifecycle costs, and prolong the service life of flat roofing installations.
Implement Pull-Out Testing on Your Next Project
By integrating pull-out testing into the construction process, stakeholders can ensure the reliability, compliance, and long-term sustainability of flat roof installations, ultimately delivering superior outcomes for building owners, occupants, and communities alike. Take Tecron’s advice: don’t discover the importance of pull-out testing by accident.
Tecron: Your Roofing Partner
For full details and information on our range of Single Ply membranes please contact the Tecron Team or call and see us at our trade counter. Alternatively, email our team via sales@tecron.ie or call us on +353-91-353545.
The Benefits of Single Ply Membranes in Modular Construction
In Ireland and across the world, modular construction has emerged as a dominant trend: a game-changing approach that combines speed, efficiency and sustainability like no other. Single Ply Membranes are among the most popular roofing solutions in modular construction, and with their huge range of benefits, it’s not hard to see why. In the latest learning resource from Tecron, we explore the benefits of single ply membranes including PVC, EPDM, TPO & FPO.
The superior properties of these membranes have propelled their market growth. Here at Tecron, we’ve observed this growth in popularity first-hand, particularly in more specialist projects due to their levels of adaptability.
The Advantages of Single Ply Membranes
Let’s take a look at each of the advantages of Single Ply Membranes on modular construction projects in greater detail. If you’re in a rush, you can jump straight into the range of mechanically fixed, fully adhered and roof finish products we have to offer.
1. Adaptability Meets Flexibility
Single Ply Membranes are popular thanks to their incredible level of versatility, with their ability to adapt to a broad range of modular construction designs and configurations. That’s why we’re seeing these systems being rolled out on a large scale across residential, commercial and industrial facilities.
2. Low Weight, High Performance
One of the key strengths behind modular construction is its sheer agility, driven by the efficiency and mobility it allows. Thanks to their lightweight, easy-to-handly nature, Single Ply Membranes can contribute to this speedy process.
With modular construction projects being primarily assembled off-site and transported to the final location, Single Ply Membranes further streamline transportation, logistics and installation processes.
3. Easy to Install
With time being the most valuable resource in modular construction projects, Single Ply Membranes can significantly increase the pace at which the roofing process can be completed. This is because these systems can be prefabricated to fit specific dimensions, thereby reducing on-site cutting and welding.
Beyond that, the flexibility of Single Ply Membranes facilitates faster, more streamlined installation, cutting labour costs and construction timelines along the way.
4. Enhanced Longevity & Durability
Those working on modular buildings will be only too aware of the impacts of transportation stresses and environmental factors. This is why Single Ply Membranes provide a significant advantage due to their exceptional durability, allowing them to withstand the harshest of weather conditions; as well as UV radiation and temperature fluctuations.
When it comes to longevity, these systems have a proven record, with a life expectancy of over 50 years. Indeed, that 50-year lifespan involves minimum hassle as no fixing is required.
5. Sustainability, Efficiency & Integration with Green Technologies
Embodied carbon in construction is currently responsible for 15% of global greenhouse gas emissions. With this alarming statistic in-mind, sustainable practices are becoming increasingly important. Single Ply Membranes offer major benefits in this area, contributing to the energy efficiency of a building as a whole.
There are a few reasons to consider why these systems are so efficient. Firstly, Single Ply Membranes ensure no loss of heat through ingress of water or drafts thanks to their watertight properties. This reduces heating and cooling costs through minimised energy consumption. Secondly, Single Ply Membranes can be supplied in a range of lighter colours which can offset any solar gain; further reducing any cooling requirements during summer months.
Aside from their energy efficiency, these membranes are generally seen as a more environmentally friendly choice compared to traditional roofing systems. This is because they can be recycled at the end of their lifespan, reducing environmental impact and promoting circular economy principles.
Finally, Single Ply Membranes provide a seamless platform for integrating green technologies such as solar panels and green roofs, offering a stable and compatible roofing substrate.
6. Low Maintenance Requirements
Minimalistic and cost-effective maintenance strategies are one of the core principles that underpin modular construction today. This is a key factor driving the popularity of Single Ply Membranes, which require little ongoing maintenance and hassle-free upkeep compared to traditional roofing systems.
Whilst these systems are low-maintenance, ensuring regular inspections and cleaning can preserve their integrity in the long-run.
Single Ply Membranes: A Modular Essential
As the construction industry continues to embrace modular methodologies, Single Ply Membranes are poised to play a pivotal role in shaping the future of
construction practices. Be sure to check out our Single Ply Membranes page to access a range of expert resources, from brochures and technical sheets to BBA certificates, drawing details and more.
Tecron: Your Roofing Partner
For full details and information on our range of Single Ply membranes please contact the Tecron Team or call and see us at our trade counter. Alternatively, email our team via sales@tecron.ie or call us on +353-91-353545.
Understanding the Importance of High-Quality Vapour Barriers
A vapour barrier is a material designed to prevent the movement of moisture-laden air from passing through the building envelope. It helps control condensation and moisture-related issues.
Using a high-quality vapour barrier in a roof build-up can offer several benefits that contribute to the overall performance, longevity and energy efficiency of a building.
Why a High Quality Vapour Barrier Matters
Here are some of the key benefits of using a high-quality vapour barrier in a roof build-up:
Moisture Control
One of the primary functions of a vapour barrier is to prevent moisture from entering or exiting the building envelope. Moisture infiltration can lead to issues like mould growth, rot and deterioration of building materials. A high-quality vapour barrier effectively controls the movement of water vapour thus reducing the risk of moisture-related problems.
Condensation Prevention
In our cool damp climate, warm indoor air can carry moisture that, when it comes into contact with colder surfaces within the roof assembly, can condense into liquid water. This can lead to structural damage and insulation performance degradation. A vapour barrier minimises the chances of condensation by blocking the movement of warm, moisture-laden air into the colder parts of the roof assembly.
Improved Energy Efficiency
Moisture infiltration can compromise the insulation’s thermal performance, causing it to become less effective at maintaining indoor temperatures. By preventing moisture from entering the insulation layer, a vapour barrier helps maintain the insulation’s R-value, resulting in improved energy efficiency and reduced heating and cooling costs.
Enhanced Durability
Moisture can weaken the structural integrity of building materials over time. With a vapour barrier in place, the risk of moisture-related deterioration, such as wood rot or corrosion of metal components, is significantly reduced. This contributes to the long-term durability of the roof assembly.
Air Quality and Health
Moisture infiltration can create a conducive environment for mould growth, which can lead to poor indoor air quality and potential health issues for occupants. A vapour barrier helps prevent the conditions that promote mould growth, maintaining a healthier indoor environment.
Prevention of Thermal Bridging
Some insulation materials can lose their thermal resistance when exposed to moisture. A vapour barrier protects insulation from becoming damp, preventing thermal bridging and ensuring consistent thermal performance across the roof assembly.
Protection of Roof Components
Moisture can damage roofing components like decking, timberwork, and even structural elements, leading to premature failure and increased maintenance costs. A vapour barrier shields these components from moisture-related damage, prolonging their lifespan.
Insurance against construction flaws
Even if the initial design of the roof assembly does not anticipate significant moisture infiltration, environmental factors and construction flaws can still lead to moisture-related issues. A vapour barrier acts as an “insurance policy” providing an additional layer of protection against unforeseen moisture problems.
Conclusion
When selecting a vapour barrier, it’s essential to consider factors such as the climate zone, the roof assembly’s design, the type of insulation used and the local building regulations. Using a high-quality vapour barrier that is compatible with the specific requirements of the roof build-up will help maximise the benefits outlined above and contribute to the overall performance and longevity of the building.
Got a Question? Ask Tecron
For more in-depth roofing insights, trust Tecron. Tecron’s Technical Team can aid in the design and delivery of the optimum roofing solutions for your upcoming roofing project. To get started, contact us at sales@tecron.ie, call us on +353-91-353545 or follow us on LinkedIn.